
Collaborative Condition Monitoring and distributed AI in machine tools
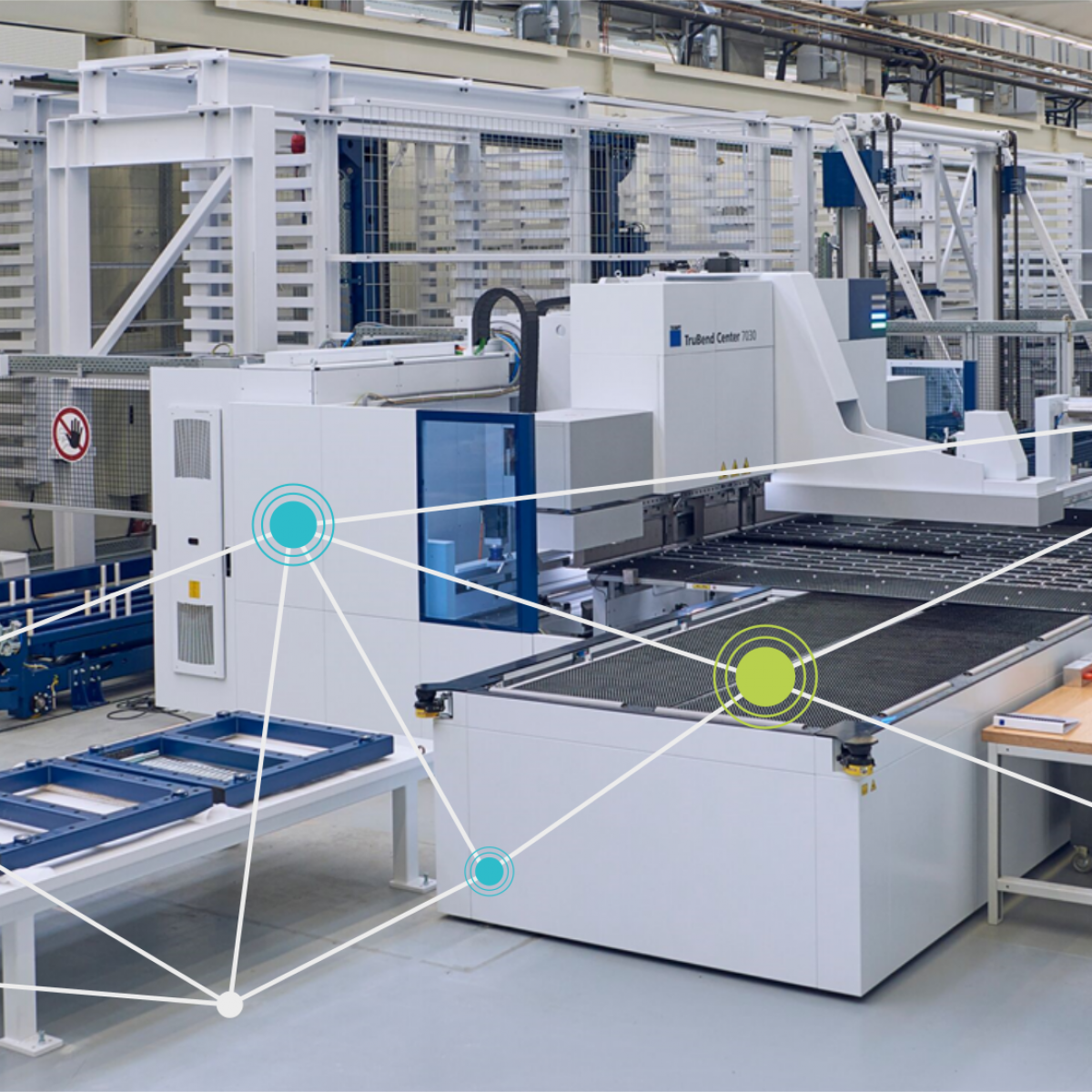
Vision
Operators of modern machine tools place the highest demands on machine availability and reliability.
Quality deviations in the manufacturing process due to incipient wear or a malfunction cannot be clearly assigned to a part or component using existing approaches to preventive and predictive maintenance.
Manufacturers, operators and users of modern machine tools therefore need to understand the quality-determining interaction of a large number of installed components and the machine tool itself, recognise changes in condition at an early stage and proactively avoid production downtimes.
With ProKInect, we aim to demonstrate collaborative condition monitoring with diagnostic capabilities in secure data spaces.
Goals
Data confidentiality
Cooperative learning of AI agents in shared data spaces.
Transparency
Mutual exchange of information between AI agents of all actors with interpretable models.
Autonomy
Distribution of manufacturer- or component-specific AI agents spatially and across different across different hierarchy levels of the machine tool.
Results
Digitalization in production technology allows for efficient machine condition monitoring using sensors and IoT. Data analysis reduces costs by enabling precise maintenance planning and minimizing machine downtime. Collaborative condition monitoring promotes new business opportunities and enhances production processes through shared data and insights. One major obstacle in data sharing is the concern over data privacy and security, as companies are wary of exposing sensitive information to potential competitors. Additionally, the lack of standardized data formats and interoperability issues between different systems can significantly hinder effective data exchange.
The BMBF joint project “ProKInect”, which is one of 17 ProLern initiatives, aims to implement a manufacturer-independent condition monitoring system. The sub-goals include developing new collaborative business relationships that go beyond traditional bilateral partnerships, secure and trustworthy data exchange in protected data spaces, and the integration of expert and user knowledge into AI models. The project participants include TRUMPF, WITTENSTEIN, TVARIT, and the Fraunhofer LBF.
This whitepaper discusses the fundamental principles and objectives of collaborative condition monitoring. It also describes the concept and presents a specific case study.
Prognostics and Health Management (PHM) is a key factor for the profitable integration of production machines into digitalised production systems. Condition monitoring, remote diagnosis and the early detection of critical deviations from the process window are required for a stable digitised value creation process, in order to be able to monitor them sufficiently early and in a differentiated automated manner. Strictly data-based approaches fall far short here, as essential information about technical interactions of the causal failure states cannot be taken into account or recorded when setting up condition monitoring and failure diagnosis. However, the implementation of a model-based approach requires detailed knowledge of the physical interactions of the failure mechanisms, which is often difficult to realise for reasons of complexity and expense.
The research project ProKInect focuses on collaborative condition monitoring with distributed AI agents. It addresses the cross-company development and use of condition monitoring systems for production facilities. Such cross-stakeholder development still presents a challenge. This white paper outlines the steps taken in ProKInect in a sequence that demonstrates how this challenge can be met.
Digitalization in production enables efficient machine monitoring through sensors and IoT. The BMBF-funded ProKInect project aims to implement a manufacturer-independent condition monitoring system. Challenges include data protection and lack of standardization.
The basics
Condition monitoring detects machine deviations at an early stage and optimizes maintenance. AI methods such as machine learning and fuzzy logic analyze sensor data and predict conditions. ProKInect uses adaptive neuro-fuzzy systems and possibilistic logic to manage uncertainty.
Case study
A TruLaser laser cutting machine is used as a test platform. AI agents analyze motor current, speed, and sensor data. PySyft ensures secure data transmission and processing. An FMEA identifies error sources and exclusion criteria for accurate diagnosis.
Conclusion
ProKInect demonstrates the effectiveness of possibilistic symptom evaluation and AI agents. Challenges such as sensor variability and data interpretation remain. Future research focuses on real-time analysis and federated learning to improve privacy. Ethics and transparency remain key issues.
ProKInect has made progress in AI-based condition monitoring by combining physical models, neural networks, and fuzzy logic. Secure data processing using PySyft and accurate fault diagnosis using FMEA were critical. Future integration of additional data sources and ethical AI design promise further improvements.
Partners
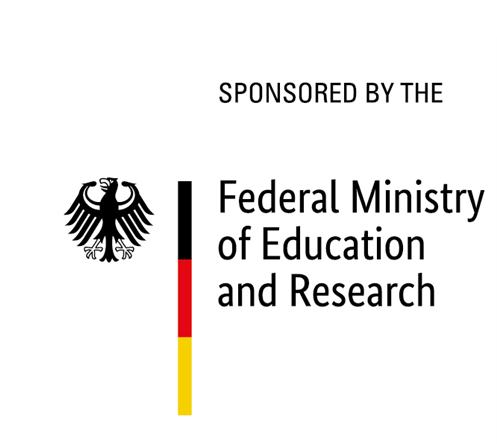
Contact
- Fraunhofer Institute for Structural Durability and System Reliability LBFBartningstraße 47 64289 Darmstadt
- +49 6151 705-0
- jonathan.millitzer@lbf.fraunhofer.de