Fraunhofer LBF
As a research institution, the Fraunhofer Institute for Structural Durability and System Reliability LBF investigates issues in the field of structural durability and system reliability. The scientists at Fraunhofer LBF use a variety of methods to model complex failure-effect relationships and make statements on system reliability and criticality using mathematical models. Fraunhofer LBF’s work is motivated by the question of how the expert knowledge gathered can increase the explainability of AI-based condition monitoring and maintenance systems. The idea of directly integrating knowledge into an AI system based on the wealth of experience of the production and maintenance teams in the companies and the designers at the plant manufacturers is a motivating factor here. As a result, both the software architecture of the monitoring approach and the AI models themselves can be designed to be knowledge-based and interpretable for users and operators. Robustness, reliability and performance of the system are key aspects, as is the consideration of dependencies resulting from variable production operations and feedback from maintenance. The use of AI models based on expert knowledge also enables differential diagnoses of various causes of faults and increases the accuracy of maintenance measures.
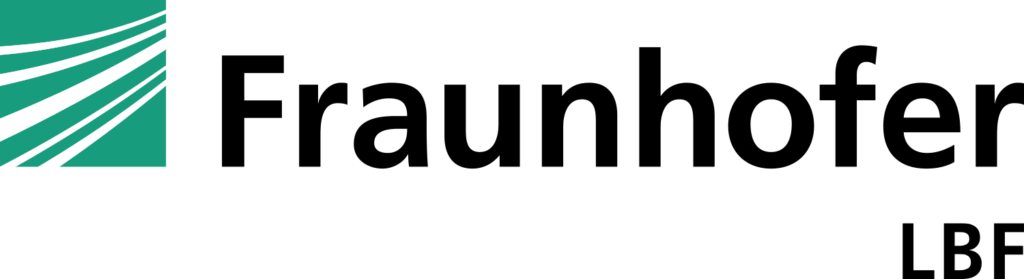
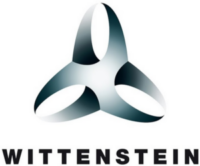
WITTENSTEIN SE
WITTENSTEIN SE’s sensorised drive technology is already capable of operating in digital value networks thanks to Industry 4.0 connectivity and the product twin using the asset administration shell. Digital services from WITTENSTEIN make it possible to record drive train data over the product lifetime, monitor it for anomalies and communicate with higher-level components.
In ProKInect, WITTENSTEIN is pursuing the goal of creating opportunities for secure data exchange in value creation networks and increasing manufacturing productivity with the help of AI.
TVARIT GmbH
Tvarit GmbH is a young company that is driving digital transformation by developing AI-based business models. The AI experts at Tvarit provide software and hardware platforms for integrating AI methods into Industry 4.0 applications. They specialise in signal processing methods and machine learning for Industry 4.0 solutions in manufacturing and process industries. Tvarit’s areas of application are very diverse. A past project, for example, was the quality prediction and calculation of dynamic recipes in aluminium coil production, more precisely in the rolling process, taking into account process parameters such as strip speed and rolling pressure as well as the prediction of tool wear for drilling machines. Another project was the combination of condition monitoring and predictive maintenance to predict tool breakage in precision tools for metal cutting. Here, for example, Tvarit was able to use tools more often by predicting the remaining service life. In addition, corrective action recommendations were given for a longer tool life. Tvarit is always endeavouring to develop robust and scalable AI methods and to make the AI applications even more user-friendly and easier to use.
For this reason, the company is actively researching in the areas of machine learning and signal processing, always with the aim of improving overall efficiency in manufacturing industries. Tvarit has been recognised by repeated awards as the most innovative start-up in Germany (TiE Deutschland 2018) and as one of the eight best out of 490 AI companies across Europe (EDI EU-Horizon 2020).

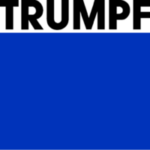
TRUMPF SE + Co. KG
At TRUMPF, powerful status diagnostics functions based on drive signals are already being realised for series machines. In addition to the individual evaluation of data from individual machines, this data is also analysed statistically and using machine learning methods. As not all relevant status information is contained in the drive signals, an increasing number of sensors are being integrated into TRUMPF machines to increase the reliability of machines and processes, including MEMS sensors in sensor networks with decentralised intelligence. In order to enable reliable status diagnoses and forecasts based on the available signals, AI methods are to be used to a large extent in the future, which will lead to manageable solutions even for very complex cause-effect relationships. As part of product development for the autonomous factory (smart factory), TRUMPF is already working intensively on the use of AI to support operators in the use of highly complex products and processes and thus optimise customer benefits. In addition, there are initial products in the field of autonomous sensor-supported process control in real time and initial experience in the field of AI-supported detection of tool wear conditions.
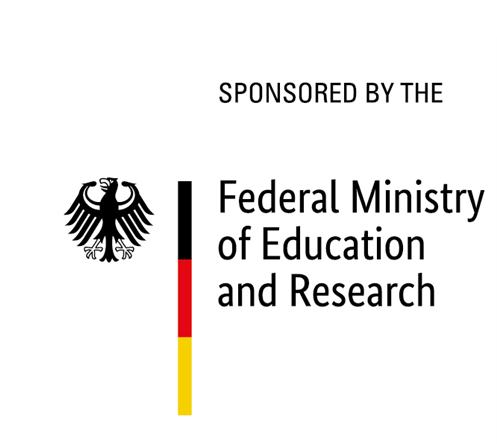
Contact
- Fraunhofer Institute for Structural Durability and System Reliability LBFBartningstraße 47 64289 Darmstadt
- +49 6151 705-0
- jonathan.millitzer@lbf.fraunhofer.de